3D nyomtatott dugattyúkat tesztel a Porsche a GT2 RS-ben
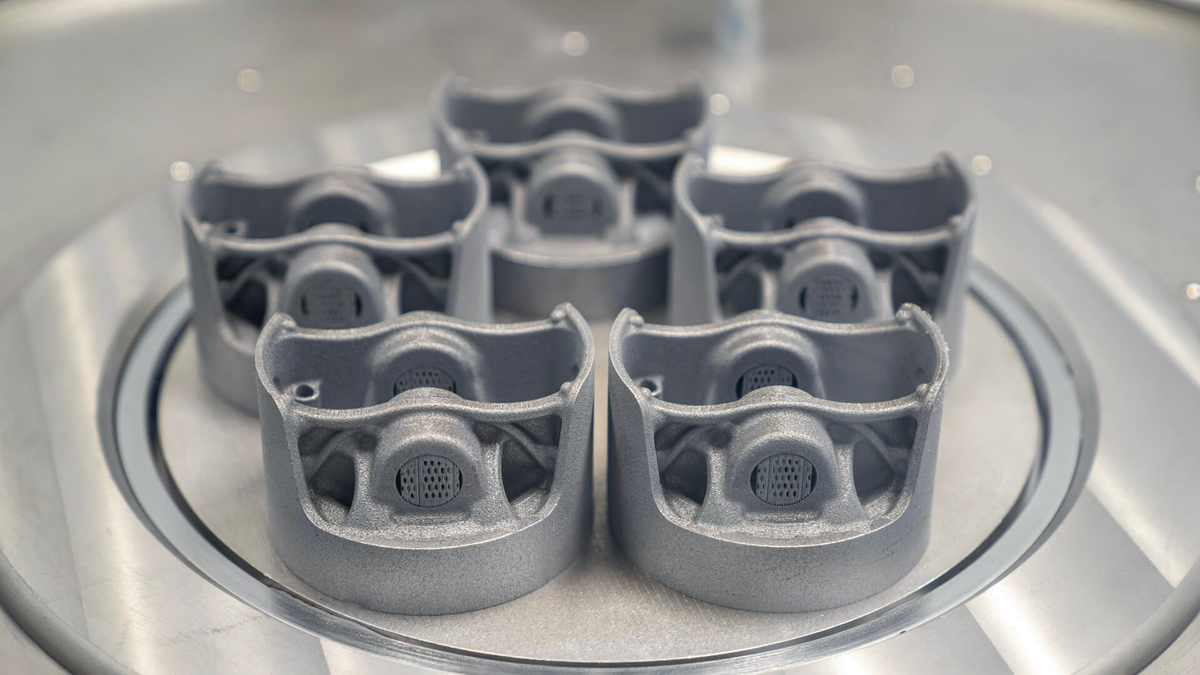
A beszállító partnerekkel végzett közös munka eredményeképpen előállított dugattyúk sikeresen vették az első próbákat.
Nem ez az első alkalom, hogy a Porsche mérnökei a 3D nyomtatást a gyakorlatban alkalmazzák. Az úgynevezett additív gyártási módszer segítségével előállított kagylóülések például május óta már szériában elérhetőek a 911-esek és a 718-asok vásárlói számára, akiknek ezáltal még arra is van lehetőségük, hogy az ülések keménységét a saját preferenciáiknak megfelelően kiválasszák. A sportosabb élményt kedvelők a keményebb, a kényelmet előnyben részesítők a puhább, a kompromisszumkészek pedig a közepes keménységű változatot is megrendelhetik. Emellett a Porsche Classic műhelyében számos olyan acél, alumínium és műanyag alkatrészt állítottak már elő 3D nyomtatással, amelyek már nem voltak elérhetőek az oldtimerek karbantartásához vagy javításához.
Ez a gyártási mód mind technikai, mind gazdasági szempontból nagy jelentőséggel bír, hiszen egyedi, kisszériás vagy a motorsportban használt alkatrészeket is könnyebben, gyorsabban, mindig épp az adott igénynek megfelelően lehet vele előállítani. A szaknyelven additív gyártási módszernek hívott háromdimenziós nyomtatással szinte bármilyen forma előállítható akár egyetlen példányban is. Nincs szükség egy minimális rendelési mennyiségre a gyártás beindításához, az egyszerre legyártott nagyobb mennyiséget nem kell raktározni, nincs szükség öntőformák vagy présszerszámok legyártására és raktározására, így a kész tervek és 3D modellek birtokában bármikor, igény szerint előállítható egy-egy példány a kívánt alkatrészből.
Az gyártási és logisztikai előnyökön kívül fontos előrelépés a tervezésben, hogy 3D nyomtatással olyan formák is létrehozhatók, amelyek a hagyományos öntött vagy préselt alkatrészek esetén egyszerűen nem megvalósíthatóak, plusz az így elkészített darabok az optimális felépítés miatt egyszerre tudnak még könnyebbek és erősebbek is lenni.
A prototípus gyártás és az egyedi pótalkatrészek után a Porsche úttörőként lépett előre abba az irányba, hogy teljesítménynövelés céljából is alkalmazza ezt a technológiát: a cél az volt, hogy GT2 RS csúcsmodell 700 lóerős teljesítményét még tovább tudják növelni.
A dugattyúk anyaga egy speciálisan erre a célra a Mahle berkein belül kifejlesztett ötvözetből készült alumíniumpor, amelyből 1200 rétegben, 12 órás folyamat során építi fel a nyomtató a teljes modellt. A tervezés során az eredeti modellen szimulációkat futtattak le, amelyek segítségével sikerült meghatározni, hogy az új, rugalmasabb gyártási folyamat során az alkatrész mely pontjain lehet kevesebb anyagot használni a teherbírás csökkentése nélkül – ahol eddig csak a korábbi gyártástechnológia miatt nem tudták ezt megtenni – és hol szükséges tovább erősíteni a szerkezetet. Az optimalizálással 10%-kal sikerült csökkenteni az egyes dugattyúk tömegét, miközben a nyomtatásnak köszönhetően egy olyan hűtőcsatornát is ki tudtak alakítani, amely nagy terhelés mellett is akár 30 fokkal tudja csökkenteni a hőmérsékletet.
A kisebb tömegnek, az alacsonyabb hőmérsékletnek és az égési folyamat ezek által elérhető további finomhangolásának köszönhetően magasabb fordulatszámot tudtak elérni változatlan hatékonyság mellett, így a korábban 700 lóerős motor teljesítménye további 30 lóerővel emelkedett.
A Porsche, és a projektben együttműködő beszállító partnerei – a dugattyúgyártásban nagy névnek számító Mahle, a fémnyomtatókat tervező Trumpf, valamint a merőeszközöket fejlesztő Zeiss – a többféle elérhető nyomtatási technológiából a Laser Metal Fusion (LMF – porágyalapú lézeres olvasztás) elnevezésű változatot alkalmazták, amelynél a kamrában elterített port a kívánt kontúr mentén rétegenként olvasztja meg a lézernyaláb, így rétegről rétegre építi fel az alkatrészeket.
Az így készült alkatrészeket a nyomtatást követően megtisztítják a fel nem használt fémportól, majd a hagyományos eljárással készült dugattyúkkal azonos megmunkálási és ellenőrzési folyamaton vezetik végig őket. A hőkezelést és felületkezelést különféle tesztek követik, amelyek között pl. vizuális mérésekkel ellenőrzik a mérethelyességet, CT-vel – azaz komputertomográffal – megröntgenezve keresik a repedéseket vagy egyéb anyaghibákat. A minőségellenőrzésen sikeresen átesett példányok kerülhetnek végül a hathengeres boxermotorokba, amelyeket a jelenlegi teszt során egy 200 órás tartóstesztnek vetettek alá, ebből pedig 135 órán keresztül teljes terhelésen kellett hibamentesen teljesíteniük az elvárt normákat. Mivel a kísérleti projekt sikeresnek bizonyult, a közeljövőben vélhetően egyre több hasonló megoldással találkozhatunk majd a Porsche belsőégésű motorokkal szerelt változataiban.